In pharmaceutical and chemical manufacturing, some of the biggest threats are the ones you can’t see. Invisible or low-level exposure to potent active ingredients, often as airborne particles or vapors can quietly accumulate and harm workers over time. As new drugs and chemicals become more potent, the demand for robust containment is rising. Chronic exposure to hazardous compounds has been linked to long-term health damage, and even minimal exposure can trigger serious consequences. To manage these invisible threats, the industry relies on two key tools: Occupational Exposure Band (OEB) and Occupational Exposure Limit (OEL). These classifications help assess how dangerous a substance is and guide what containment strategies or high-containment systems are required to handle it safely.
What Are OEB and OEL?
In simple terms, OEB and OEL are frameworks for evaluating and controlling hazardous substance exposure in the workplace. Occupational Exposure Band (OEB) is a category rating of a substance’s potency or hazard potential. A higher OEB means a more toxic substance, which in turn demands stricter safety measures and containment systems. Companies, often classify compounds from OEB 1 (lowest hazard) up to OEB 5, or even OEB 6 in some schemes, to quickly communicate how careful one must be when handling a given material. This banding approach is especially useful early on, for example when a new Active Pharmaceutical Ingredient (API) is in development and a formal limit isn’t established yet. Saying “this is an OEB 4 compound” immediately signals the need for heavy precautions, without having to quote an exact microgram value.
Occupational Exposure Limit (OEL), on the other hand, is a specific numeric limit on exposure. It’s typically defined as the maximum concentration of a substance in air (often measured in µg/m³ or ppm) that workers can be exposed to during an 8-hour shift without significant health risk. In essence, OEL is the quantified safety threshold derived from toxicological data, the level at which no acute or chronic damage to health is expected for the average worker. OEL values are set by regulatory bodies (for example, OSHA in the US or the European Chemicals Agency) and are backed by research on each substance’s effects. In practice, if OEB is the hazard category, the OEL is the precise benchmark. Knowing a compound’s OEB guides the initial containment strategy and equipment selection, while the OEL provides a concrete target for monitoring exposure and ensuring it remains under control.
Practical Interpretation of the Classes
What does all this mean for your actual production setup? In practical terms, the OEB or OEL number assigned to a compound dictates the level of containment required. The attached hazard classification chart illustrates this clearly.
Here’s how to interpret the OEB classes in terms of workplace controls:
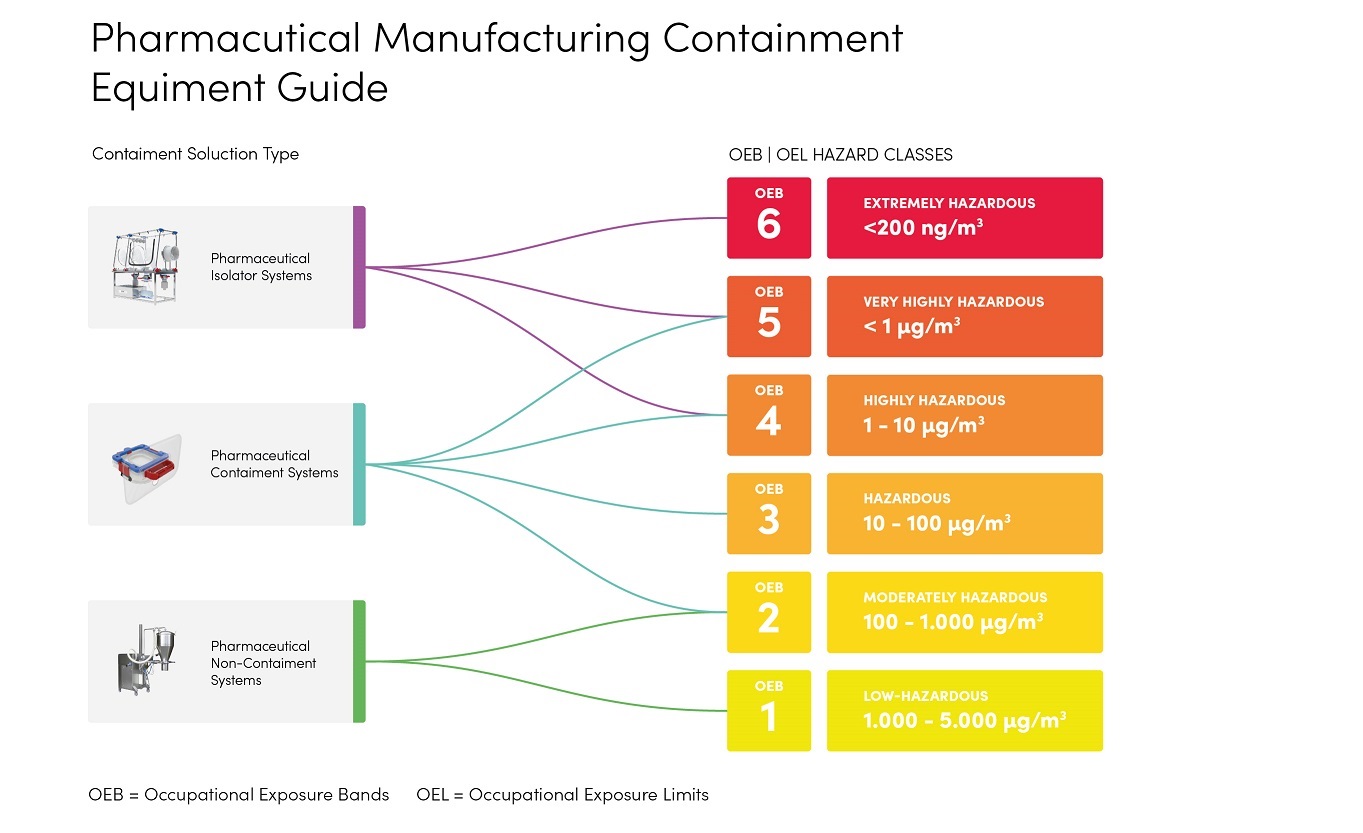
Full Screen
Substances in OEB 1–2 are considered to have relatively low toxicity (often described as “harmless” or almost so). Open handling in standard facilities is generally acceptable for these materials. Basic precautions like good general ventilation and routine personal protective equipment (PPE) may suffice. In other words, at this level the process can, often remain in an open system without special containment enclosures, as long as normal lab safety practices are followed.
At OEB 3 or 4, we enter the realm of potent compounds that can cause harm with unprotected exposure. Handling should not be completely open. Containment systems are recommended – for example, using closed transfer devices, local exhaust ventilation, or continuous liner systems (also known as endless liners) when transferring powders. These measures create a barrier between the operator and the product. For instance, companies, often employ glove bags or continuous liner drum transfer systems at OEB 3 (10–100 µg/m³) to safely remove or charge materials without releasing dust. By OEB 4 (around 1–10 µg/m³), even stricter controls like hard-shell gloveboxes or enclosed charging stations become prudent. The goal is to prevent any dust, aerosol, or vapor from escaping into the workspace, since the substance is hazardous even in tiny quantities.
Using OEB/OEL classifications in this way helps to align the risk level of a substance with the appropriate engineering controls. By knowing the band (and the corresponding OEL range), engineers and EHS officers can determine whether a process can be done on an open bench, needs a containment enclosure, or requires a top-level glovebox isolator. It’s a practical roadmap for safety.
The manufacturing of Highly Potent Active Pharmaceutical Ingredients (HPAPIs) is a rapidly growing sector, driven by the increasing demand for targeted therapies, particularly in oncology. HPAPIs are characterized by their ability to elicit therapeutic effects at very low doses, necessitating stringent containment measures to protect both personnel and product integrity. As a result, many pharmaceutical companies are partnering with specialized Contract Development and Manufacturing Organizations (CDMOs) that possess the requisite expertise, facilities, and regulatory compliance to safely handle and produce these compounds. These CDMOs offer advanced containment technologies and adhere to rigorous safety protocols to ensure the safe development and commercialization of HPAPI-based therapies.
Implications for Your Process Installation
Implications for Your Process Installation
Underestimating exposure risks in a pharma process can have severe consequences – for both people and the operation itself. Firstly, there’s the direct human cost. If a compound calls for containment and you handle it in the open, you are effectively treating your operators as the filters. Some effects might be immediate: for example, one industry publication noted that an operator working unprotected with a strong sedative (hypnotic API) could become drowsy or impaired before the end of a single shift. The same goes for potent hormones or oncology drugs – even small exposures can cause acute symptoms. More, often, though, the effects are insidious. Many hazardous substances won’t cause noticeable illness right away, but chronic low-level exposure can lead to cumulative poisoning, respiratory issues, organ damage, or cancers years later. This is why controlling those “invisible” exposures is so critical. The health of your team is on the line, and so is morale – no one wants to work in an environment where they feel unsafe or may develop occupational illnesses.
There are also operational and legal implications if you get containment wrong. A contamination or exposure incident can derail production: imagine having to halt a batch because a potent powder escaped and spread in the room, requiring an extensive cleanup and possibly medical checks for staff. The downtime and lost output (not to mention potential batch scrap) can be very costly. Beyond that, regulators are watching. Authorities like OSHA and their international equivalents enforce exposure limits strictly. In one case, a pharmaceutical company was fined over $250,000 by OSHA after workers complained of being exposed to hazardous dust and were found literally covered in powder. The investigation revealed the firm hadn’t implemented the necessary protections. No company wants to be in that position. The legal obligation to protect employees is clear: employers must provide a safe, healthful working environment and shield employees from known hazards. Failing to meet established OEL requirements can result in citations, hefty fines, or even shutdowns until issues are corrected. In short, proper containment isn’t just a technical preference – it’s both a moral duty and a compliance mandate. By investing in the right containment solutions for your OEB/OEL needs, you protect your people, avoid costly disruptions, and stay on the right side of the law.
ROMYNOX as Your Containment Partner
Ensuring effective containment for hazardous compounds requires the right mix of expertise and equipment. This is where ROMYNOX can help. We provide a full range of containment products to match any OEB class, from isolators for OEB 5–6 scenarios to flexible options for mid-level hazards like OEB 3–4. This includes Ezi-Dock CSV Systems the high containment powder transfer solutions, and rapid transfer ports. Our solutions integrate easily into your existing setup, ensuring safe, efficient, and fully contained processes.
Most importantly, we bring deep knowledge of containment strategy. Our specialists work closely with you to assess risks and recommend the appropriate level of containment. We have helped numerous clients upgrade their facilities for potent product handling, and we can share real-world examples upon request.
Ready to improve your containment strategy? Get in touch with ROMYNOX today.