The pharmaceutical industry is under constant pressure to operate more efficiently, safely, and flexibly. Single-Use technology is no longer just a trend but has become the industry standard for addressing these challenges. The transition from stainless steel systems to single-use components has fundamentally transformed the development and production of biopharmaceutical products. ROMYNOX plays a crucial role in this shift by providing high-purity solutions and supporting customers throughout the transition.
From Innovation to Industry Standard
Single-Use systems started as a niche solution but have now become indispensable in biopharmaceutical processes. The technology was developed to enhance flexibility, accelerate batch changeovers, and minimize contamination risks. Today, most biopharmaceutical companies rely on single-use bioreactors, filters, and process assemblies. Regulatory agencies, such as the FDA, support their use, primarily due to the increased product safety and quality control they provide.
Sierk van der Veen, an expert with extensive experience in single use technology and high purity processes, says that flexibility is one of the system's greatest strengths. "For customers it is essential to quickly adapt and scale their processes without being constrained by complex reusable systems. Single use enables this while also delivering a higher level of safety and efficiency."
The advantages are clear: reduced cleaning requirements, lower validation costs, faster production ramp-up, and greater flexibility in manufacturing capacity. This makes single-use an ideal choice for both clinical and commercial production.
Quality, Reliability, and Validation
One of the key considerations with single-use systems is maintaining the highest levels of quality and purity. Since components are used only once, each item must meet 100% of the specifications upon delivery, with no opportunity for re-cleaning or reuse. Pharmaceutical companies must be able to trust that every bag, tube, or connector is safe, sterile, and performs its intended function. This requires stringent quality controls from suppliers of these products. To ensure this ROMYNOX operates an advanced ISO 7 Class C cleanroom, and employs trained specialists who ensure that the assembly and validation of single-use products meet the highest standards.
According to Laura Sluijter, who has extensive experience with cleanroom processes and high-purity assemblies, the controlled environment is crucial to ensuring the reliability of single-use systems. "The process begins with a clean product that is assembled in a sealed environment. This minimizes the risk of contamination and ensures that pharmaceutical companies can operate with confidence."
Another important aspect is validation. Pharmaceutical companies must demonstrate that single-use components do not impact product quality. This involves testing for extractables & leachables and performing integrity tests such as leak detection and sterilization.
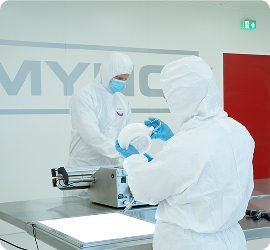
Sharief Sahebdin, Sales Engineer Single-Use at ROMYNOX, observes that more and more companies are transitioning to single-use due to the simplicity of validation. "With stainless steel systems, extensive cleaning validations are required to demonstrate that no residues or contaminants remain. Single-use components come with certificates and validation documentation, which makes the process much more efficient."
Custom Solutions and Material Selection
Single-use applications vary widely – from small research setups to large-scale production lines. Each process step may have unique requirements. Custom solutions are therefore often essential to optimally integrate single-use technology. Elmar ten Kate, who focuses on technical design and process optimization within the team, emphasizes the importance of a visual approach: "By using drawings and sketches, we can clearly show customers what their single-use system will look like. This not only helps them better understand what they’re getting, but also prevents errors in the cleanroom." A standard set of hoses or filters is not always sufficient; sometimes components need to be specially configured or assembled for a specific application. This is where expertise comes into play.
Additionally, the choice of materials plays a critical role. Not all plastic materials are suitable for every pharmaceutical process. Chemical compatibility, temperature resistance, pressure tolerance, and biocompatibility are key factors in making this choice.
Sustainability and Waste Management
A pain point of single-use technology is sustainability. While stainless steel systems last for decades, single-use inevitably generates a constant stream of plastic waste. Companies are therefore seeking ways to reduce this waste, such as by implementing recycling programs for used materials or transitioning to more sustainable plastics. Through a strong commitment to sustainable business practices, such as ISO 14001 certification and participation in the ISO 14001 certification and participation in the CO2 performance ladder, ROMYNOX contributes to the responsible implementation of single-use technology in the pharmaceutical industry.
Within the industry, there is ongoing debate about the true impact of single use on sustainability. Elmar views it as a step in the right direction: "Single-use eliminates the massive consumption of chemicals and water required to clean stainless steel systems. From that perspective, it is often a greener solution than people assume." On the other hand, Laura emphasizes the amount of waste generated by single-use. "After a single production batch, you're left with bins full of plastic. Even when using more sustainable plastics, most materials remain non-reusable. This is a challenge the industry needs to address."
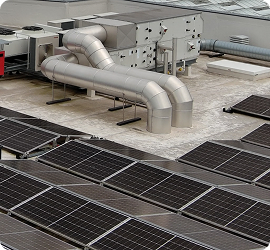
What is certain is that there is a search for more sustainable alternatives. Suppliers are developing biodegradable materials and improved recycling systems. At the same time, there is exploration of hybrid systems, where single-use components are combined with reusable infrastructures to reduce waste.
The Future of Single Use
Single-use technology continues to evolve with improved materials, more sustainable processes, and advanced automation. This not only increases efficiency but also makes the technology more versatile and reliable. According to Sierk, the rise of personalized medicine and cell and gene therapies demands more flexible manufacturing methods. "Single-use enables these innovations without the costs and complexity associated with traditional setups."
Additionally, hybrid production systems, where single-use is combined with existing stainless steel infrastructures, are gaining popularity. This offers companies flexibility without being fully dependent on single-use components.